DIP COATING
The dip coating of substrates with photoresist can be an alternative to other coating techniques if either the type or size of the substrates to be coated are not suitable for spin coating or spray coating, or the photoresist represents a significant cost factor and requires a minimisation of the coating consumption per substrate. The following section describes the technology of dip coating and provides explanations and answers to common problems associated with this coating process.
Principle of dip coating
Basic principle of dip coating
In dip coating, the substrate is usually drawn vertically from a flask filled with lacquer (figure below). The formed lacquer layer initially flows downwards in the saturated solvent atmosphere directly above the lacquer bath under the influence of gravity . Only when sufficient solvent has evaporated from the coating layer formed does the thinning of the coating film end due to the increase in viscosity. This allows the coating film thickness to be adjusted via the dwell time of the coating film in the saturated solvent atmosphere and thus via the drawing speed of the substrate (high drawing speed=high coating film thickness).
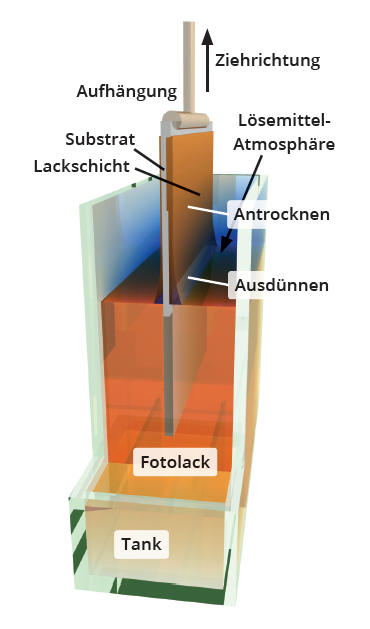
Schematic representation of the dip coating of a substrate with photoresist.
Possible advantages of dip coating
Dip coating is a sensible alternative if the size, weight or geometry of the substrates do not allow the photoresist to be spun on. The very high resist yield with dip coating (100% or 50% if only one substrate side is to be coated ) can be an important cost advantage in processes where resist consumption accounts for a large proportion of the total costs. However, it should be borne in mind that the high coating yield may make it necessary to replace the coating volume in the flask if the shelf life of the coating is exceeded before it is used up.
Limits of dip coating
Dip coating is not useful for applications in which the back of the substrates or the holes in them must not be filled with lacquer , which is technically almost impossible to avoid when dipping . Substrates with strong textures or macroscopically three-dimensional components on which large quantities of lacquer can run off over the substrate that has just been coated, leading to an inhomogeneous coating pattern, are problematic.
Technical realisation
In the case of separate, mechanically rigid substrates, they can be drawn vertically from a flask. Continuous roll-to-roll coating can also be the choice for coating films , where the substrate is pulled from a roll through a basin filled with coating and then wound back onto a roll after drying.
Equipment requirements
Tank
For the coating of individual substrates (wafers, metal sheets, etc.), the cuvette - i.e. the tank for the photoresist - should not be more than a few cm larger than the substrate to be coated in all three spatial directions; the amount of resist required to fill the cuvette is limited. This is particularly advantageous for not too large quantities of components to be coated, as the entire coating volume remaining in the flask should be replaced once the coating has reached the end of its residual shelf life. In the case of roll-to-roll coating, it is also advisable for cost reasons to estimate the amount of coating required for coating within the remaining shelf life of the coating when defining the coating volume in the tank. The walls and seals must be permanently chemically stable against the solvents contained in the dip coating, for which Teflon, HD-PE or stainless steel are suitable. For longer breaks between coating, a tightly closing lid on the cuvette minimises the evaporation of solvent or the entry of particles.
Filling with photoresist and service life
After filling a cuvette with resist, it is advisable to leave the basin to rest overnight before the first coating in order to allow the air bubbles to outgas upwards. If there are numerous defects in the lacquer layer, this may be an indication that there are still air bubbles in the lacquer. Dip paints are usually heavily diluted with solvents, which - especially at room temperature - reduces the service life. After just a few months, it may be necessary to replace the paint volume completely (not just partially!) to prevent the transfer of aged paint to the fresh batch. A measurement of the concentration of the low-boiling, more volatile solvent carried out in certain cycles enables the quantity lost through evaporation to be replenished promptly. Such a measurement can be carried out either via the viscosity of the coating or, at least for a rough estimate, via its density, as low-boiling solvents such as acetone or MEK usually have a significantly lower density than the coating in its original composition.
Substrate suspension
The upper substrate suspension should not be immersed in the lacquer in order to prevent the lacquer from flowing over the already lacquered surface of the substrate which leads to an inhomogeneous coating pattern.
Motor and control unit
The motor for pulling out the substrates must work continuously and vibration-free, otherwise there will be strong inhomogeneities in the coating layer thickness formed, which usually appear as a horizontal stripe pattern. For the same reason, the dip coater should be vibration-free. The range of possible drawing speeds is approx. 1 - 20 mm/s, typical drawing speeds are 3 - 10 mm/s.
Protection against particles
The atmosphere of the room in which the dip coater is located should be as particle-free as possible, as any impurities concentrate in the cuvette over weeks and months and lead to an intolerable coating pattern even in processes that are less critical in terms of particles. Between coatings, a lid minimises the evaporation of solvent from the cuvette and the entry of particles.
Suitable photoresists for dip coating
When selecting a suitable dip coating for a specific application, as with any lithography process, it must be clarified whether a positive, reverse or negative resist is to be used and for which resolution and with which properties the developed resist mask is to be used. The solvent composition of the lacquer is decisive for the coating result: Low-boiling solvents increase the viscosity of the lacquer layer just formed within seconds and thus prevent the lacquer from flowing too much over the substrate. High-boiling solvents prevent the coating from drying too quickly and allow the coating to be smoothed within minutes at room temperature.